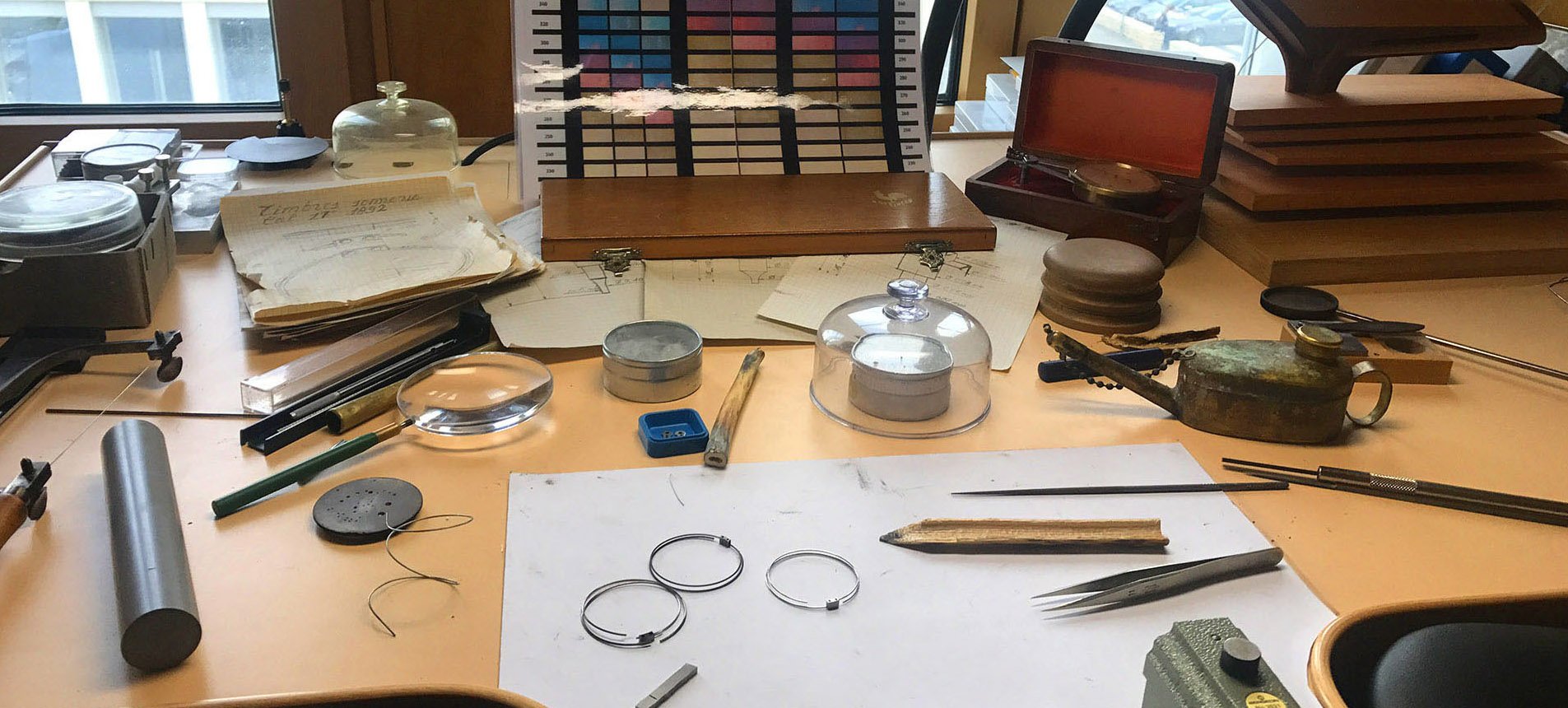
Dreams to reality
Unlike many, we do not engage any external design consultants to design our products or a main contractor to source our supply chain. While this may require more effort and time, we believe it results in a superior product. Each component is tailor-made to work seamlessly together, which is difficult to achieve with external help.
We've developed relationships with high-quality manufacturers and oversee every step of the process, from design to production. All aspects, including 3D modelling, renders, animations, shop drawings, photos, and videos, are completed in-house. We take pride in having complete control over the entire product design process, from start to finish.
Watch bracelet end link CAD drawing
Bonjour Fabien.
Notre maître.
Where others take their Saturdays leisurely, you will find Fabien, our head assembler, hard at work in his factory in Switzerland. Horology has been a part of his family tradition for four generations, and he has been assembling watches all his life, following in the footsteps of his father and grandfather. Fabien's son has also embraced the craft, adding to the family's expertise and passion. Despite his grey hair, Fabien's hands are as steady as ever, a testament to his decades of experience.
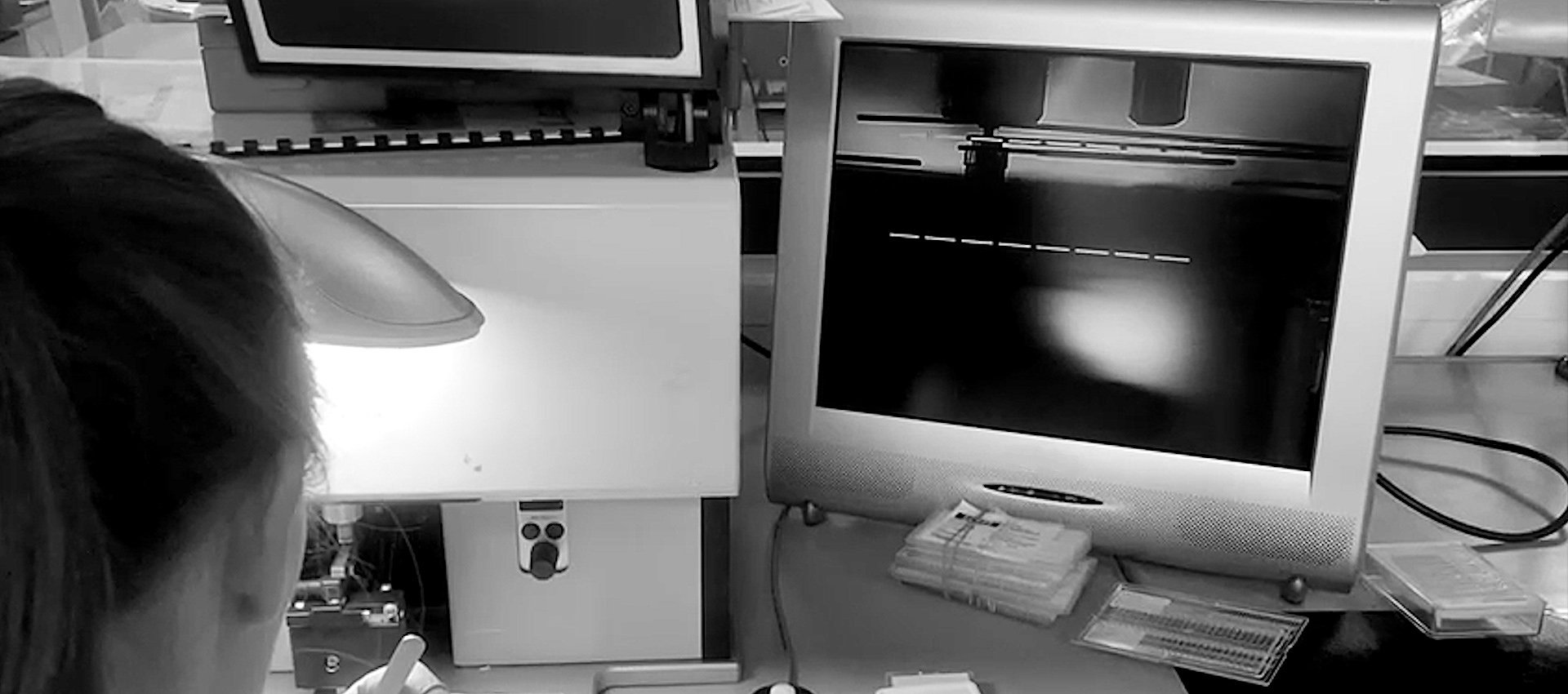
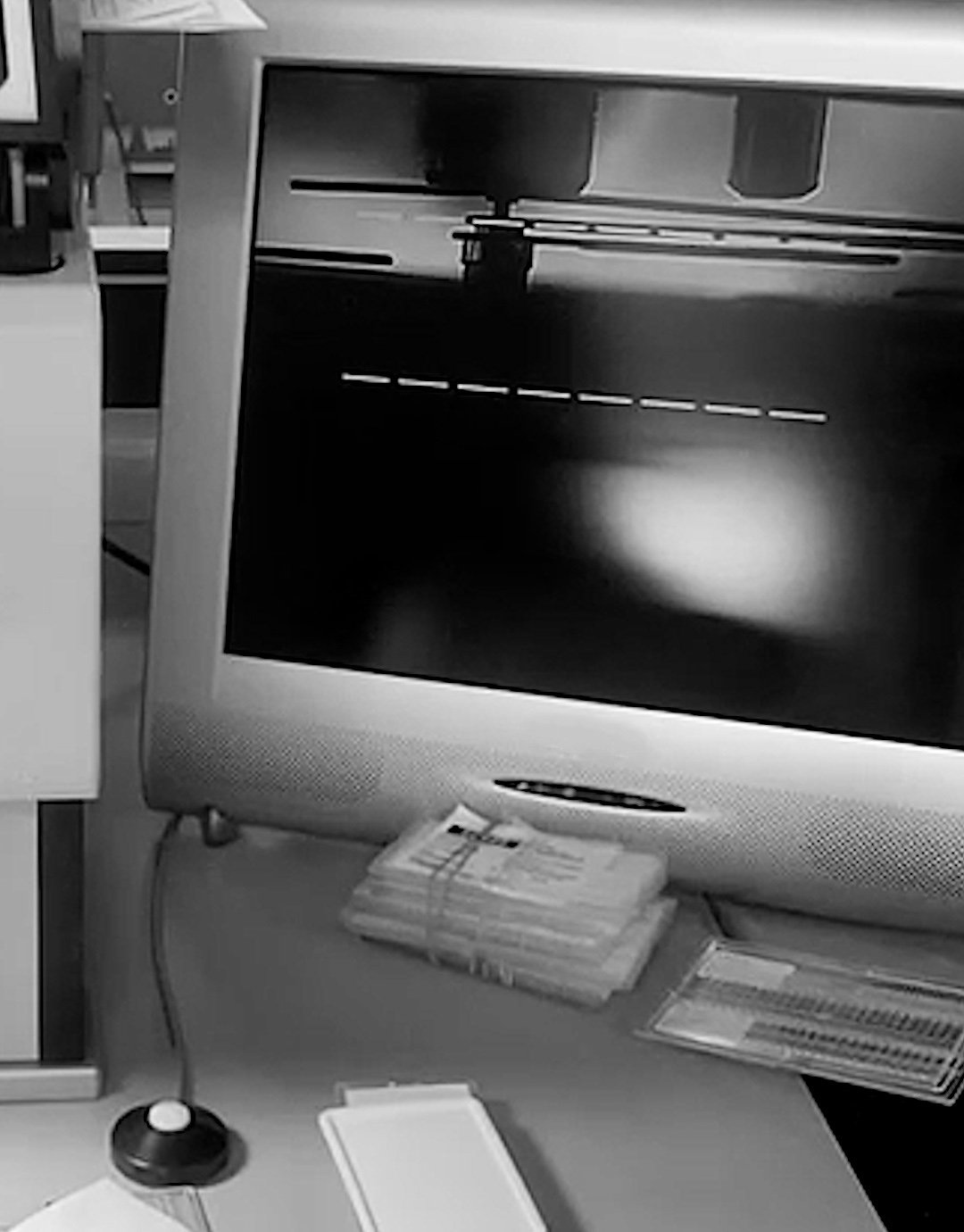
Specialized machine hand fitting. Monitor displays hands in sideview. Operator checks if there are sufficient gaps between hands so they would not clash on to each other as they turn.
The same expertise as the major Swiss watch manufacturers
This is the place where some of the most renowned Swiss luxury brands are assembled with the same level of expertise. A trusted confidant in the industry, it’s a tradition upheld with pride.
-
Watch case crystal press tools
-
A watchmaker's workbench
-
Watch components assembly in progress
-
Watch movement’s accuracy check with a timegrapher
Transparent Pragmatism
At the heart of our approach lies transparency. We scoured numerous factories in search of the right partners and built a supply chain that ensures we deliver the best quality and value to you. To achieve this, we cast our net wider and avoid restricting ourselves to a single location. We manufacture, source components, and services from trusted partners in Hong Kong, Japan, and Switzerland.
Watch case polishing / finishing floor
Our components are then sent to our partnered assembler in Switzerland, where they are meticulously assembled into a beating timepiece with the utmost attention to detail. Once the assembly is complete, our watches undergo rigorous quality control before being shipped to our warehouse in Sydney, Australia for stock-taking.
When an order is placed, the watch undergoes a final quality inspection before being carefully encased in a presentation box and dispatched from our warehouse in Sydney to customers worldwide.
-
Silicone / rubber injection mould machines
-
Silicone / rubber injection mould machines
-
6-axis CNC grinding & finishing machine
-
Bronze plate rolls stacked prior dials stamping